Introduction
Supplier Management is the process of identifying, acquiring, and managing resources critical to an organization’s operations. When products or services are developed for your company, a buyer-supplier relationship is formed. This relationship specifies the kind of working relationship you should try to establish with your suppliers. All managers involved in purchasing and supply should have a solid foundation in supplier relationship management. A well-defined governance model that promotes a two-way, mutually beneficial buyer-supplier relationship via trust and accountability is the optimum supplier management method.
Organizations that use their supply chain as a competitive advantage outperform their peers by 70%, and 79% of “leaders in the supply chain” reported revenue growth that was “substantial” and higher than the industry average. Supplier management is a strategic practice that helps your company achieve its goals while maximizing the value of supplier contracts, whether those benefits be solid, long-lasting partnerships, more affordable services, or enhanced performance. Supplier relationship management is the systematic process a business uses to evaluate the contribution and influence suppliers on success, find strategies to improve their performance and create a strategic plan to implement what has been found.
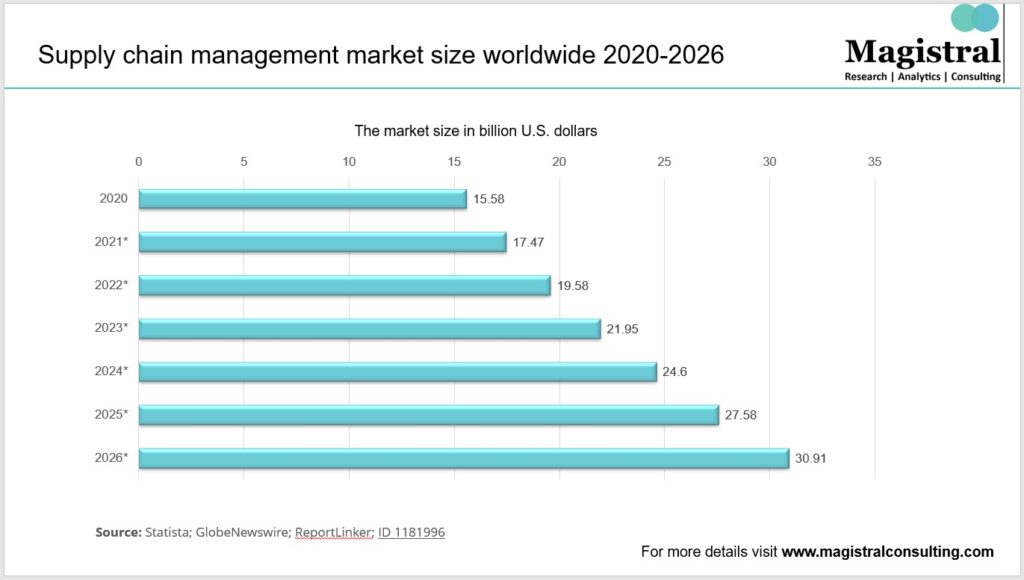
Supply Chain Management Market Size Worldwide 2020-2026
The worldwide Supply Chain Management (SCM) market is anticipated to increase from USD 28.9 billion in 2022 to USD 45.2 billion by 2027, with a Compound Annual Growth Rate (CAGR) of 9.4% from 2022 to 2027. The main market drivers are the desire for more openness and visibility in supply chain data and procedures and the rapid expansion of retail and eCommerce. Additionally, technological advancements are transforming the supply chain sector, and incorporating artificial intelligence capabilities into S.C.M products would present excellent business potential for S.C.M companies.
Importance of Supplier Management
Before we delve further into the topic it is important to ask why is supplier management so important in an organization’s scheme of things. This is because an effective supplier management system enables the effective selection of the right vendors. Besides, it helps in controlling costs as well as taking steps to better manage the onboarding process. It also helps in preventing disruptions caused by various factors in the supply chain. In this way, supplier management assumes significant importance specially in IT, Retail, and Manufacturing companies where the scale of the supply chain is immense. Here are a few benefits of supplier management explained further:
-Better Selection: By this process, one can select between a variety of vendors who put the bid, and the organization can select the best which matches their money’s worth.
-Better Contract Management: By ensuring this system, one can have a look at the centralized view of the current status of all the contracts and other information which is useful for the organization in better decision making, which enables to be more organized and saves on time.
-Better Performance Management: It helps in viewing the performance of all the vendors. This gives a better picture of what is working and what is not! Which again helps in achieving better efficiency and improves the overall performance of the organization.
-Better Vendor Relationship: It is difficult to maintain relationships with various vendors at the same time, some vendors may be fruitful for the organization whereas others might not. Getting all the information of different vendors under the same head helps in improving the decision-making.
-Better Value: Ultimately, the goal of the whole Supplier Management system is to have better value for your money. If it is done properly, then it reduces one’s cost and helps in creating more worth of the money spent.
Challenges associated with Supplier Management
There are several challenges associated with having a proper supplier management system. They are listed below:

Supply Chain Challenges
Arriving at the right group of vendors:
In large retail companies like Amazon, there can be thousands of vendors that need to be managed. Handling such a large group and ensuring that they are the right fit for the company can be a herculean task. This is where an efficient supplier management system is required.
The complexity of handling tasks:
As we have seen earlier managing a large number of vendors can be quite challenging. This is handled by a supplier management system that handles them by categorizing them vis money spent by them, strategic importance, risk management, and other such relevant factors.
Risk:
Risk mitigation, wherein risks to organization and compliance and security risks need to be managed effectively and minimized is a key challenge associated with this.
Contract management:
Most organizations enter into yearly or multi-year contracts with organizations to fulfill their needs. Managing the contract terms and adherence to the terms laid in the contract is a facet of business that an efficient supplier management system addresses.
Managing costs:
Many companies do not focus on the long-term aspects of handling a business namely relationship management and redesigning processes which are more effective in managing costs than shorter-term strategies which are purely focused on cost-cutting.
Delivering value:
Effective supplier management also results in designing innovative products and services on this front. These are critical to companies that thrive on innovation. A holistic focus on delivering value should be emphasized on rather than pure cost cutting.
Lack of visibility:
It always helps to have a centralized view of viewing things. This helps in better visibility, better resource allocation, and improved efficiency.
Supplier Management Process
The process of supplier management consists of various steps like business objectives and goals, criteria for supplier selection, evaluation of the suppliers, contracting with them, and then assessing their performances. These are further discussed below:

Supplier Management Process
Business objectives and goals:
Determine the business goals and objectives for which suppliers are necessary before starting your supplier management process. It will be clear what each department needs from outside sources so you can match the appropriate vendors to each demand without spending extra time and money.
Criteria for supplier selection:
The selection criteria for picking suppliers that will offer the most value for the demand must be defined after knowing the goals and needs that make supplier involvement necessary. Standard measurements include cost, prior work quality, industry recognition, legal reputation, etc. The selection criteria vary depending on the company type and its suppliers’ expectations. In addition, organizations use request for quotation (RFQs), request for proposal (RFPs), and request for information (RFIs) to choose the best suppliers, mainly when the requirements are stringent.
Evaluating and selecting suppliers:
Evaluate all relevant suppliers based on the selection criteria you have identified. Many organizations evaluate the suppliers based on the pricing they have quoted. However, factoring in the other measures one has identified is equally essential. Assess potential supplier quotations and proposals and ensure you derive maximum cost-saving opportunities. Analyze the term and conditions to see how well the suppliers plan to meet the organizational requirements.
Contracting and negotiating with suppliers:
One must carry out the contractual procedure to eventually get them on board. To gain insightful knowledge on how the contract may secure the optimum value delivery, including all pertinent stakeholders in the contracting process. Work with the suppliers to remove obstacles to a smooth negotiation process. The advantages of developing deep relationships with suppliers have been long demonstrated.
Assessing the performance of suppliers:
One must regularly assess a person’s performance after selection and onboarding to see how effectively they meet established goals and standards. Ensure you have created key performance indicators (KPIs) to measure performance and ensure practical evaluation. This will also highlight potential areas for enhancement to increase supplier performance. It also reveals the effectiveness of our supplier management approach and suggests ways to improve it.
The Future of Supplier Management
The future of Supplier Management is digital. This means having a real-time and instant view of the supply chain management system where we can see what is happening to the supply process realistically at any given point in time. This also means including more participants in the B2B transactional space thereby enabling the participants to resolve supply disruptions in a better manner.
It will also help in reducing time-consuming activities such as audits, simplifying underlying processes, and ensuring statutory compliance.
Besides this, the future is one dominated by the inclusive use of Artificial Intelligence-based platforms which will lead both to time and cost savings while at the same time making better future predictions.
Magistral’s Services on Supplier Management Process
Supplier Management is crucial to the success of an organization. Hence, it becomes important to arrive at a process of making an effective supplier management system.
-Supplier Identification & Onboarding: This includes preparation of List Building, Supplier Profiles, HSE Documentation, Contact, and Compliance.
-Dashboards & Reports: In this, dashboards are prepared around various factors like quality, timelines, and pricing of products and services.
-Relationship Analysis: In these, comprehensive reports are made to assess the relationship value.
-Custom Reports: It includes customized reports for a specific business case.
-Supplier Profiles: Profiles are created and compared on the basis of pricing, management, history, red flags, key clients, and other important information.
About Magistral Consulting:
Magistral Consulting has helped multiple companies to reduce operations costs through its offerings in Procurement and Supply Chain.
About the Author
The article is Authored by Marketing Department of Magistral Consulting. For any business inquiries, you could reach out to prabhash.choudhary@magistralconsulting.com